Patented technology
To meet specific cosmetic requirements, fasteners undergo surface treatment. Unisteel's in-house research and development capabilities enabled the development of both the UNI-SHINE® and UNI-COLOR® patents.
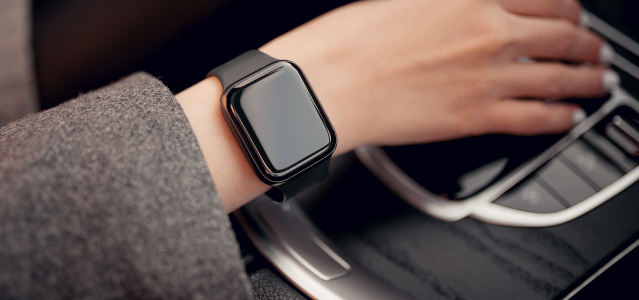
Attention to detail
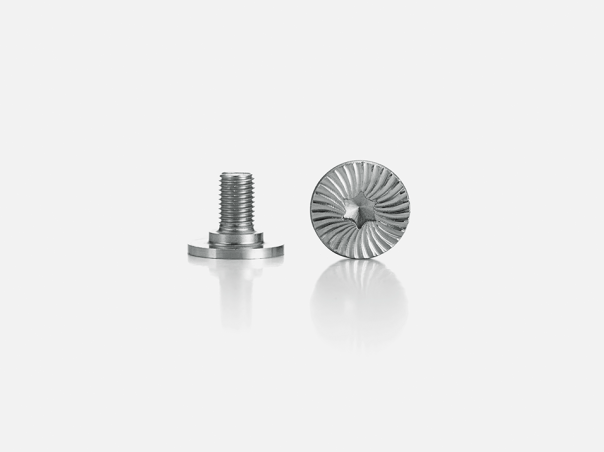
UNI-SHINE® is a proprietary texturing method which brings out the natural shine of stainless steel. It is available in different varieties and perfectly complements any precision component thanks to its high degree of compatibility with a wide range of unique patterns and textures. The enhanced metallic sheen will make any electronic device look great.
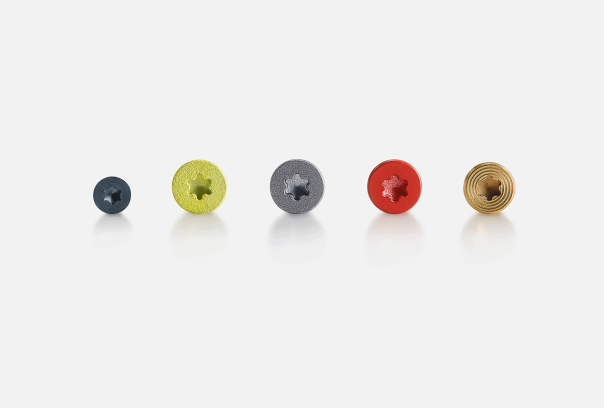
UNI-COLOR® is a special color coating that was developed to satisfy cosmetic needs and market trends. Examples of devices on which this important aesthetic feature can be found are smartphones and smartwatches. Demand for colored fastening components emerged when different colored electronic devices made their way into the market: think emerald green phones, rose gold watches, and black laptops. To date, the range of colors has been expanded beyond conventional metallic ones to Cool Jade, Pink, and Black. UNI-COLOR® is available in both spray paint and physical vapor deposition (PVD*) techniques.
Aesthetics are not the only way these products can spruce up your components: they offer excellent, long-lasting protection against wear and tear – which is inevitable in the daily use of lifestyle electronics. With adherence to RoHS standards (Directive on the restriction of the use of certain hazardous substances in electrical and electronic equipment), and being minimally pollutive, consumers can be sure that the coating will not harm their body or the environment.
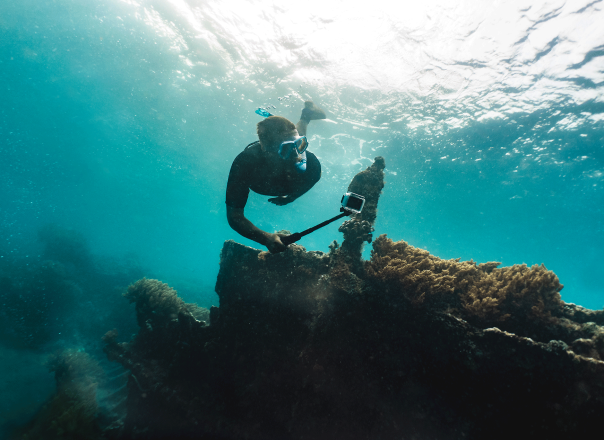
Added value as a result of cost savings
Recently, Unisteel was tasked to manufacture a product that was as shiny as possible and like a mirror to look at. Making use of the company’s existing polishing infrastructure, a series of suitable fixtures was designed. To optimize the production process, the team tried various kinds of buffing wheels and applied the polishing liquid in different positions. Eventually, they created the ideal production conditions – not just meeting the cosmetic requirements, but also providing added value for the customer as a result of cost savings.
UNI-SHINE® and UNI-COLOR® can be applied on a wide array of metal surfaces. Thanks to constant research and development, Unisteel’s team will continue to be able to exceed customers’ demands and expectations in the future. Numerous application tests are carried out on a regular basis in order to ensure that the products meet quality requirements.
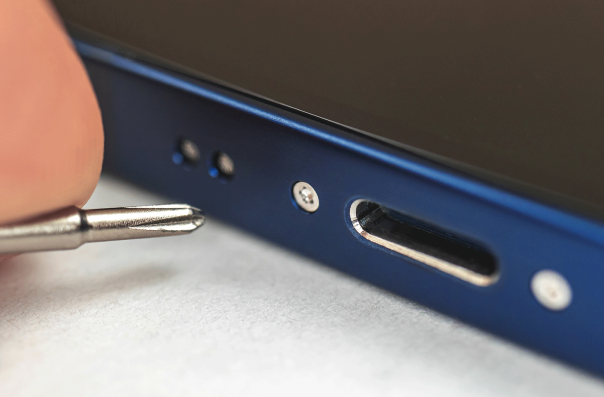
Precision component specialists
Thanks to UNI-SHINE® and UNI-COLOR®, Unisteel has further strengthened its competitive edge when it comes to demand for aesthetics in the lifestyle and consumer electronics industry. Even small details make a big difference. This patented technology has helped Unisteel’s customers to improve the design of their products and leave the end customer with an impression of luxury. Unisteel’s customers can rely on it to offer high-quality, long-lasting products in different colors and textures.
*PVD is a vacuum coating process to produce a conformal metal-based thin film with a metal, typically titanium or chromium, to be uniformly deposited on electrically conductive surfaces. A single coating layer is formed using sputter deposition, a process that provides ample coverage without modifying the surface profile. The result is a coating layer with uniform thickness, resistance to wear and corrosion, and high level of hardness. Unisteel opts for this mature technique that is used in many electronic industries including optical media, optics, and semiconductor components.